1. IIoT: Daten erfassen
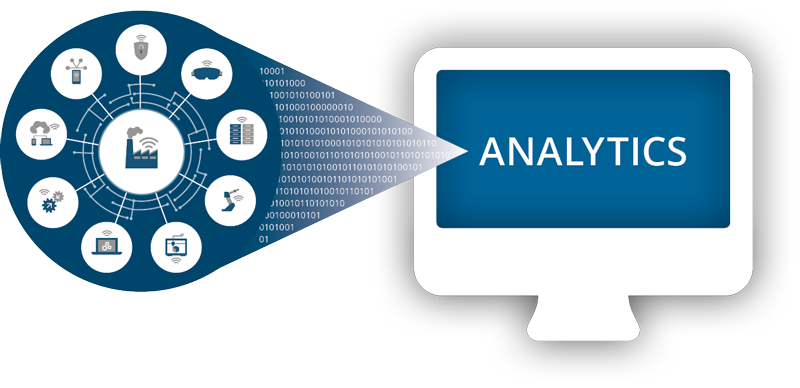
Je mehr Anlagen und Maschinen Daten liefern, desto besser können die Analytics-Möglichkeiten der Industrie 4.0 genutzt werden. Wissen Sie bereits, welche Daten vorhanden sind und wie sie erfasst werden?
Evtl. muss der Maschinenpark für eine wertsteigernde IIoT-Lösung mit passenden Sensoren nachgerüstet werden. Aber auch wenn Sie zu Beginn keinen umfassenden Kapitaleinsatz im gesamten Werk tätigen möchten, können Sie zumindest eine Produktionslinie für ein Pilotprojekt oder als Proof of Concept (POC) auswählen.
Schon kleine Schritte zahlen sich aus: Beispielsweise kann bei rückläufiger Produktionsausbeute bereits die Analyse der richtigen Daten in den einzelnen Stufen des Produktionsprozesses dabei helfen, Engpässe zu erkennen, den Ausschuss zu verringern und die Effizienz zu steigern.
Checkliste:
- Ist die Produktionsleistung verbesserungsfähig?
- Welche Anlagen und Maschinen sollten nachgerüstet werden?
- Welche Daten sind verfügbar?
2. IIoT: Historische Daten archivieren
Manche Hersteller haben zwar in ihrem Werk bereits intelligente Sensoren installiert und können Daten zum Produktionsprozess generieren, es fehlen jedoch die für eine konsequente Erfassung und regelmäßige Archivierung dieser Daten erforderlichen Systeme, Mitarbeiter oder Prozesse. Fortschrittlichere Hersteller haben dagegen bereits Lösungen für die Datenspeicherung und -analyse implementiert, mit denen sie Tausende von Datenpunkten innerhalb von bestehenden SCADA-, MES- oder ERP-Systemen erfassen können. Diese OT-Systeme speichern große Mengen von Zeitreihendaten in einem hochkomprimierten Format, das zugleich permanent für Echtzeitanalysen verfügbar ist.
Mit einer umfassenden IIoT-Strategie können Sie Daten von einer Vielzahl an Sensoren sofort miteinander korrelieren und anschließend nach den Ursachen von Systemanomalien suchen sowie ggf. entsprechende Korrekturmaßnahmen einleiten, um zukünftig ähnliche Probleme zu vermeiden.
Checkliste:
- Wie viele Daten sollen archiviert werden?
- Wo sollen die Daten gespeichert werden?
- Wie oft wird darauf zugegriffen?
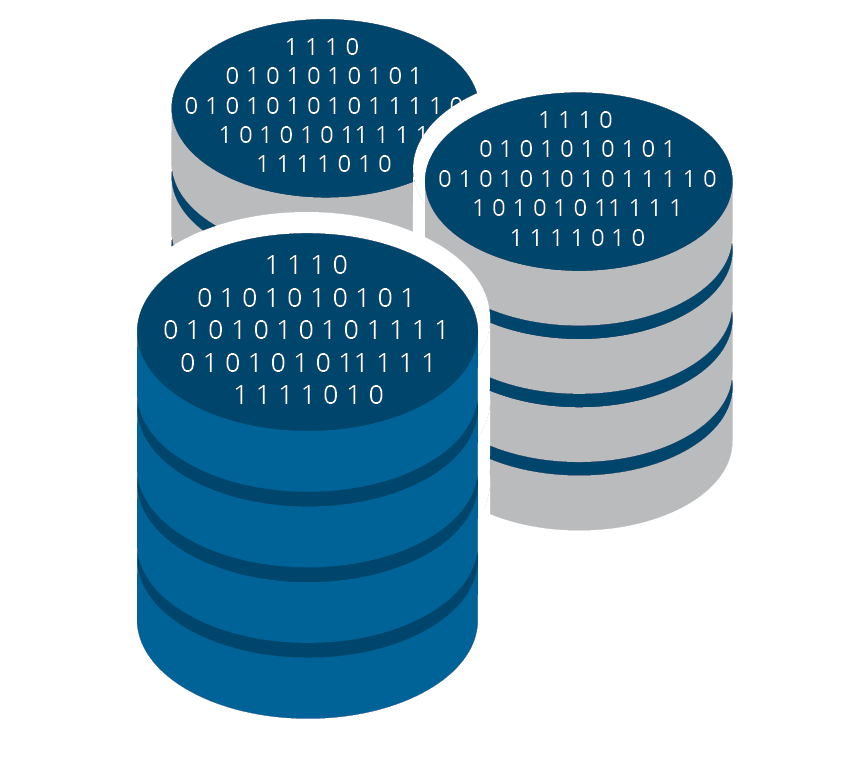
3. IIoT: Trends visualisieren
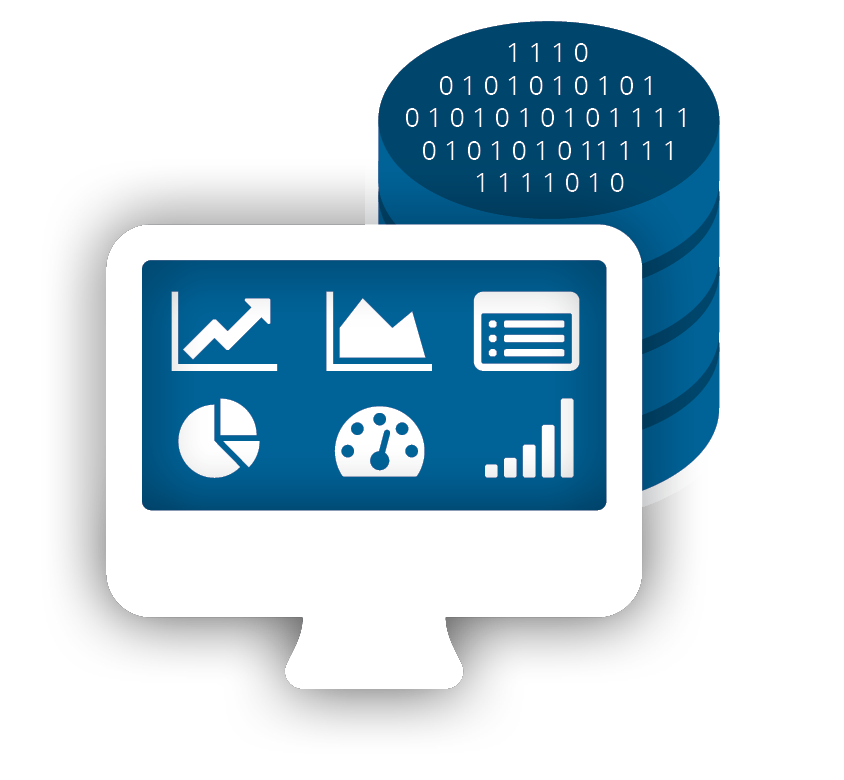
Allein die Verfügbarkeit von Daten aus Anlagen und Maschinen macht diese nicht wertvoll. Die Daten selbst sind bedeutungslos. Produzierende Unternehmen müssen imstande sein, die erfassten Daten zu visualisieren und daraus die richtigen Erkenntnisse zu ziehen.
- Self-Service-Tools: Stand-Alone-Plattformen wie z. B. Tableau oder QlikView bieten moderne Funktionen zur Visualisierung historischer Trends und Datenmuster, erfordern jedoch unter Umständen steile Lernkurven bzw. das Wissen professioneller, wissenschaftlich ausgebildeter Datenanalytiker.
- Eine praxisnahe Alternative sind Plattformen für industrielle Datenanalysen mit integrierten, benutzerfreundlichen Funktionen für die Echtzeit-Datenvisualisierung. Diese Produkte wurden für Business User konzipiert und richten sich an Unternehmen, die anstelle weiterer modularer Pakete eine Komplettlösung bevorzugen.
Checkliste:
- Wie viele Datentypen sollen visualisiert werden?
- Welche Diagramme werden benötigt?
- Sind professionelle Datenanalytiker erforderlich?
4. IIoT: Alarmmeldungen überwachen
Mit Systemen, Verfahren und Abläufen zur Echtzeitüberwachung von Schwankungen der Sensorwerte sind Hersteller in der Lage, laufende Chargeproduktionen zu korrigieren, drohende Anlagen- bzw. Maschinenausfälle zu erkennen oder ungeplante Stillstände zu vermeiden. Deshalb ermöglichen Lösungen zur industriellen Datenanalyse die Konfiguration von benutzerdefinierten Warnschwellen für jedes Gerät, jeden Sensor und jede Maschine. Abweichungen von Temperatur, Druck, Spannung, Schwingung oder Durchflussmenge lösen Alarmmeldungen aus, die dem Produktionsmanager als E-Mail, SMS oder auf dem Systembildschirm angezeigt werden.
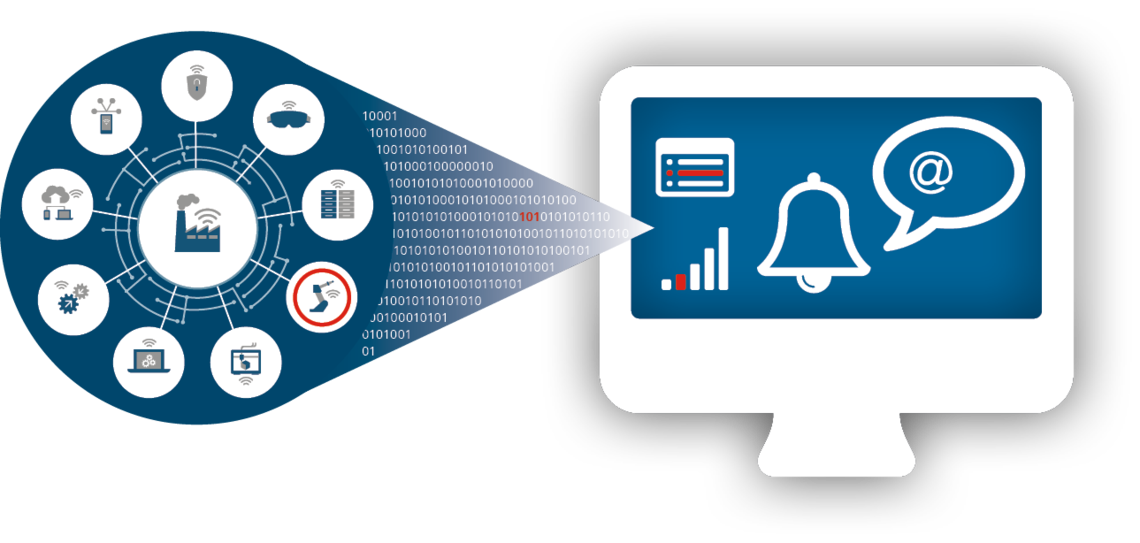
Wenn Werksleiter, Betriebsingenieure oder Wartungstechniker die Abläufe im Fertigungsbereich in Echtzeit verfolgen, überwachen und auf Alarmmeldungen reagieren können, lassen sich Maschinen- und Anlagenverfügbarkeit steigern, Arbeitsunterbrechungen reduzieren und signifikant Kosten einsparen.
Checkliste:
- Welche Anlagen und Maschinen sollen überwacht werden?
- Auf welche Schwellenwerte soll die Sensorik eingestellt werden?
- Wer soll bei Alarmmeldungen benachrichtigt werden?
5. IIoT: Produktionsleistung analysieren
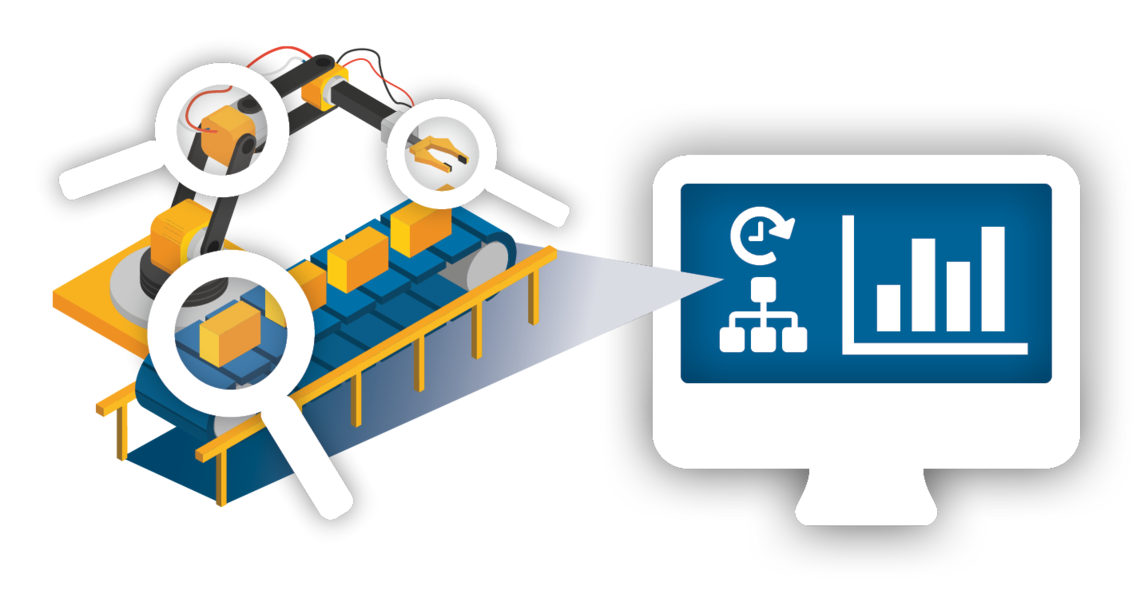
Checkliste:
- Welche Produktionslinien sollen analysiert werden?
- Kann die Grundursache eines Fehlers bestimmt werden?
- Ist die Produktionsleistung vorhersehbar?
Die Fähigkeit, die Produktionsleistung proaktiv zu verbessern, aufkommende Probleme frühzeitig zu erkennen und von der vorbeugenden zur vorausschauenden Instandhaltung überzugehen, gilt als das Nonplusultra der Industrie 4.0 und das höchste Reifestadium der industriellen Datenanalyse. Die jüngsten Fortschritte in Big Data Analytics und neue Algorithmen des maschinellen Lernens machen es möglich: Echtzeitanalyse-Lösungen, mit denen historische Trends mit zukunftsbezogenen Projektionen verglichen und Produktionsleistungen prognostiziert werden können.
Auch Ihr Unternehmen kann mit den Echtzeitanalyse-Lösungen von Intelligent Solutions Ausschuss und Produktmängel reduzieren, Anlagenausfälle und ungeplante Stillstände verhindern. Das verbessert die Rentabilität und holt den bestmöglichen ROI aus Ihrer Industrie 4.0-Strategie heraus.
Fünf Stufen der Datenanalyse in der Industrie 4.0
Lernen Sie unsere Industrie 4.0-Lösungen näher kennen!